Foam glass gravel is a unique building material that has recently gained popularity in the North American construction industry for under-slab thermal insulation. It’s produced by transforming post-consumer recycled glass into lightweight, closed cell aggregate that can be used in a variety of applications. Given the current challenges builders, engineers, and architects face in built environment construction, foam glass gravel is a future-facing solution poised to change how we think about subslab insulation.
Subslab Insulation is a core component of building construction that contributes to comfortable indoor temperatures while reducing energy consumption. Traditional insulation materials such as expanded polystyrene, cellulose, and mineral wool have been used for decades years to insulate concrete slabs, but foam glass gravel offers a more environmentally sustainable and efficient solution.
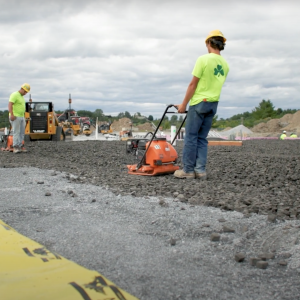
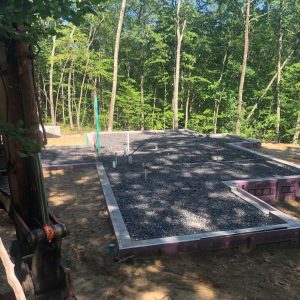
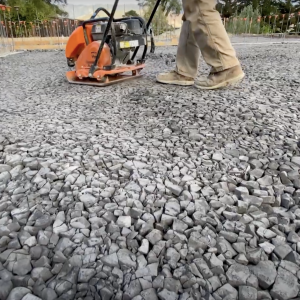
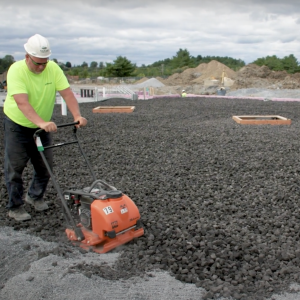
Glavel’s foam glass gravel has R1.7 insulation, so it effectively prevents heat loss in the winter, resulting in reduced heating costs. Being made from glass, foam glass gravel is fire-resistant, non-toxic, non-leaching and does not emit harmful gases or fibers, making it a safe and healthy choice for installation.
One advantage of foam glass gravel as an insulator is that it can be easily installed without the need for heavy quarried aggregate and time consuming rigid foam board insulation. It acts as a two-for-one replacement that removes both of those trades and installation logistics from slab installations. Foam glass gravel is also highly durable and doesn’t settle or compress once compacted, ensuring long-term performance and compressive strength.

Another benefit of using foam glass gravel is its environmental impact. As mentioned earlier, foam glass gravel is made from recycled glass, which reduces glass ending up in landfills. With the current state of recycling in The United States, only a third of recycled glass actually ends up being recycled. Sadly, much of the remainder goes to landfills. Foam glass gravel repairs a portion that underperforming system, diverting post-consumer glass from ending up in landfills and upcycling it into building materials.
When looking to improve building performance and embodied carbon footprint, look no further than foam glass gravel. The combination of R value, durability, in-place weight, and material composition make it a clear choice for use as a subslab insulator in the built environment.